Comment évoluer de la conception à la fabrication d’assemblages multi-matériaux en toute confiance
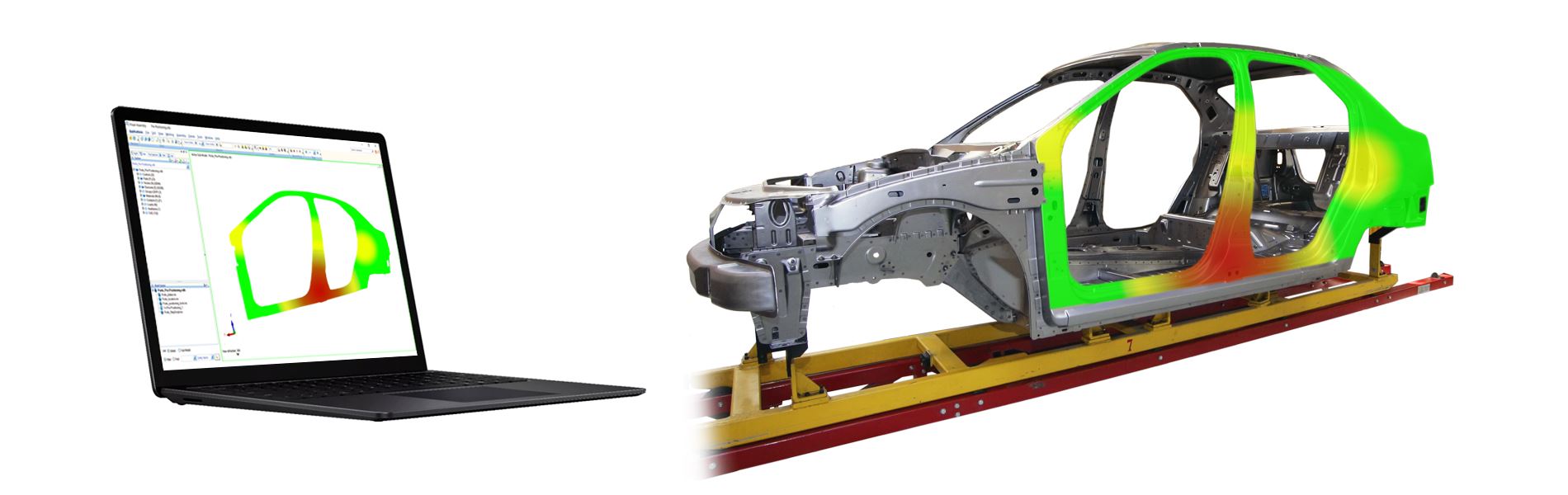
Mus par la nécessité de réduire les émissions de CO2 et par l’avènement de la mobilité électrique, les constructeurs automobiles et leurs fournisseurs se sont engagés vers le développement de produits légers, novateurs, personnalisés et durables, qui peuvent être fabriqués en grande série selon une architecture d’usine de type « lot size 1 » pour produire selon les spécifications client.
La légèreté est devenue un facteur incontournable en matière de conception de caisse en blanc, d’ouvrants et de châssis, avec le passage d’une fabrication 100 % acier à des stratégies, plus complexes, multi-matériaux qui associent aujourd’hui principalement l’acier à l’aluminium et aux composites.
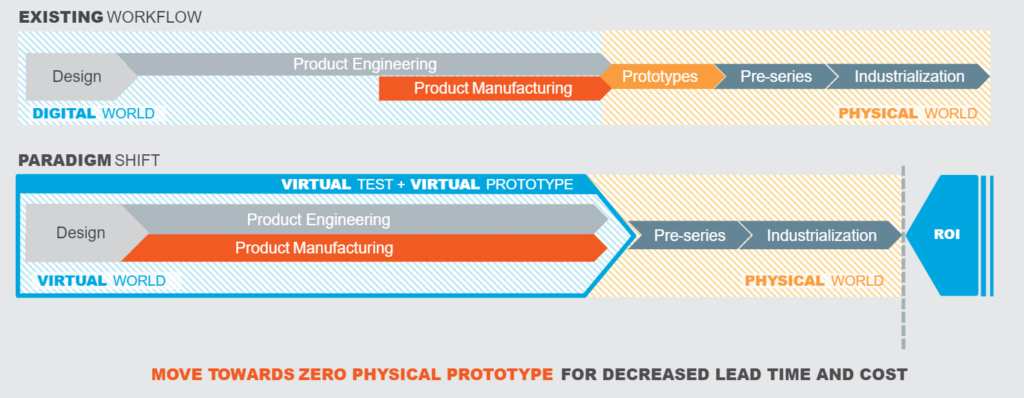
Afin de répondre au défi de l’électrification, ces assemblages multi-matériaux sont essentiels pour produire des véhicules au meilleur rapport coût-légèreté et accroître le rendement énergétique lors de la production. Toutefois, la hausse actuelle des investissements côté groupe motopropulseur a pour corollaire des investissements plus prudents côté châssis et caisse. Cette situation complexifie l’optimisation coût-efficacité, tant lors de la conception que lors de la fabrication de ces véhicules.
Passer de la simulation numérique ciblée au prototypage virtuel de bout en bout
Au cours de ces dernières décennies, la simulation numérique a été déterminante pour permettre aux constructeurs d’évaluer la faisabilité de la fabrication ainsi que pour déterminer et valider les performances du produit assemblé. Toutefois, les décisions de fabrication se prennent relativement tard dans le processus, une fois la conception figée, avec l’appui d’essais physiques. Les modifications de dernière minute et les boucles d’itération associées engendrent un risque de coûts supplémentaires et de retards de démarrage de la production.
La bonne pratique consiste à trouver une conception optimale intégrant les contraintes de performances et de fabrication aussi tôt que possible et à la valider lors des phases d’ingénierie, de façon hautement prédictive, afin de minimiser les prototypes coûteux et les modifications de conception tardives au cours de la validation de la fabrication préalable à la production.
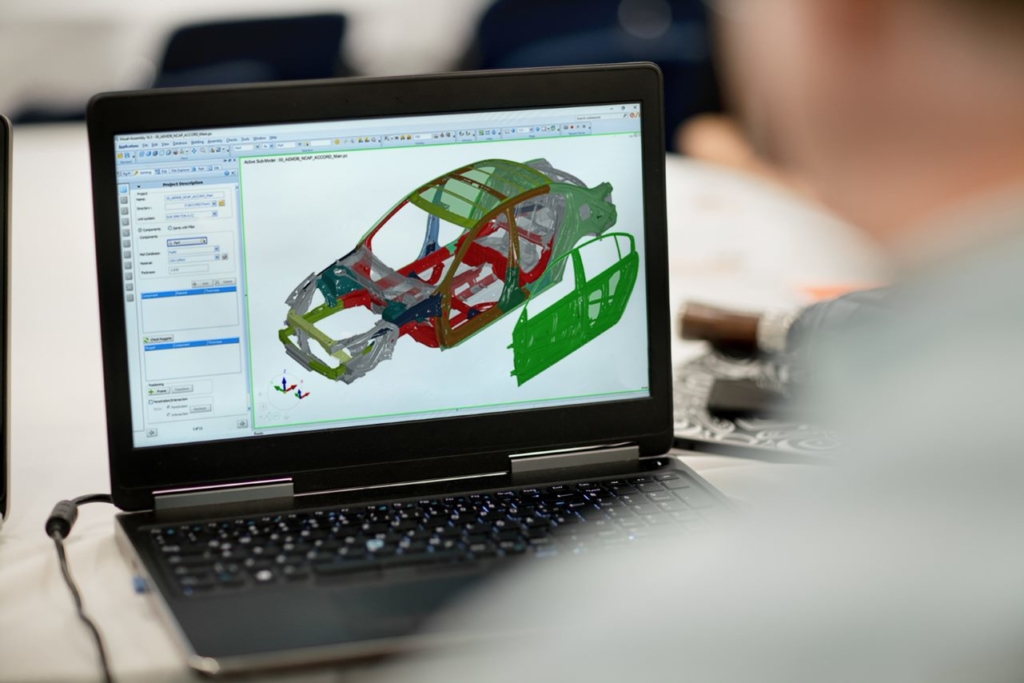
Parvenir à une conception optimale par une approche 100 % numérique n’est pas simple. Deux points essentiels sont à prendre en compte pour garantir un parcours sans accroc jusqu’à la production en série (illustration 2) :
- Fabrication de pièces unitaires : la simulationdétaillée de la fabrication de pièces unitaires intervient en général plus tard dans le processus. Avecle recours de plus en plus fréquent aux nouveaux matériaux, les constructeurs automobiles ont besoin d’obtenir très en amont des certitudes pour prendre les bonnes décisions sur l’utilisation des matériaux appropriés aux endroits opportuns. Il est donc très important de savoir estimer la faisabilité de la fabrication dès le début, dès la création des premières définitions CAO et de la première nomenclature (BOM). Le prototypage virtuel prend en compte toutes ces informations dans les phases amont, d’améliorer la prédictibilité de la simulation des performances ainsi que la simulation du processus d’assemblage – avant même la définition des outils et des matrices qui seront utilisés.
- Processus d’assemblage : les méthodes d’assemblage multi-matériaux sont nombreuses. Pour pouvoir faire le bon choix, il est crucial de modéliser et de simuler avec précision le processus d’assemblage ainsi que le comportement local des connections afin de répercuter les bonnes propriétés mécaniques issues du procédé de fabrication dans les modèles de validation des performances (crash, fatigue, etc.). En outre, les ingénieurs doivent tenir compte de l’impact du processus d’assemblage sur la géométrie des pièces afin de prévoir la qualité dimensionnelle des assemblages et leur tolérancement relative.
La vision à long terme : minimiser les prototypes physiques dans la fabrication automobile
Le prototypage virtuel constitue une approche de bout en bout permettant la validation anticipée des choix de conception, des matériaux ainsi que de la stratégie de fabrication et d’assemblage, avec à la clé des avantages considérables tout au long du cycle de développement. Son utilisation offre des certitudes avant le passage au monde physique, en donnant un éclairage net sur la stratégie de production, qui sera in fine validée virtuellement avant la production en maintenant un lien constant avec la validation des fonctions et des performances produit. Cette approche ouvre la voie vers un cycle de validation produit quasi 100% numérique où les constructeurs automobiles pourront se passer d’une grande partie des prototypes physiques, raccourcissant ainsi en final le cycle de développement produit tout en minimisant son coût et en réduisant le délai de démarrage de la production (SOP).
Nissan réduit de 50 % les délais d’ingénierie d’un nouveau matériau léger
Pour atteindre ses objectifs de réduction de poids, le constructeur japonais Nissan a étudié l’utilisation d’associations de matériaux (aluminium, acier et assemblages composites). Les ingénieurs du groupe ont fait appel à la solution de simulation d’ESI destinée à la fabrication de composites pour développer une nouvelle méthode de moulage par injection et de moulage par compression, améliorant ainsi considérablement le rendement de leurs chaînes de production. En introduisant la simulation numérique en lieu et place de la phase d’essais itératifs par tâtonnements, généralement longue et coûteuse, les ingénieurs de Nissan ont pu sélectionner de manière très précoce les types de matériaux tout en garantissant le respect du cahier des charges et des objectifs de production. De leur propre estimation, ils ont réduit les délais d’ingénierie de 50 %.
Nissan a annoncé publiquement ses avancées en matière de production de pièces en fibres de carbone. Le constructeur automobile a ramené le temps de production d’une pièce renforcée en fibres de carbone de deux heures à deux minutes, soit une diminution du temps de production d’un seul moulage de 80 %. Cette agilité technologique permet également à Nissan de produire des pièces de formes complexes, avec à la clé un gain de poids moyen de 80 kg par véhicule.
Cette prouesse a pu être obtenue essentiellement grâce à la possibilité de prendre des décisions en toute confiance et de réaliser une optimisation anticipée. Elle est aussi le fruit de la synchronisation des activités à la fois en conception et en ingénierie de fabrication pour les processus de formage, de traitement thermique et d’assemblage.
Comsol France sera présent cet été au Congrès français de mécanique 2025
Comsol, l’éditeur des logiciels Comsol Multiphysics, Comsol Server et Comsol Compiler, sera présent lors de la 26e édition du Congrès français de mécanique, qui aura lieu du 25 au 29 août prochain à Metz. Cet évènement est organisé par le Laboratoire d’étude des microstructures et de mécanique des matériaux (LEM3) en partenariat avec le Laboratoire […]
Benoît Hennaut prend la présidence du Centre d’études et de recherches de l’industrie du béton (Cerib)
Âgé de 64 ans, Benoît Hennaut a été élu le 1er juillet 2025 à la présidence du Centre d’études et de recherches de l’industrie du béton (Cerib). Il succède à Bertrand Bedel, président depuis 2021. Il est le président du directoire du groupe Herige Industries. Une carrière internationale dans le secteur de la construction Benoît […]
La simulation multiphysique au service de la fiabilité pour la microélectronique et l’opto-électronique
J’exerce mon expertise pour l’industrie à l’aide de ma maîtrise de techniques et de compétences transversales en physique, en électronique et en mécanique. Par mes connaissances en packaging & assemblage micro-électronique, en matériaux et en calcul scientifique, je développe et crée des techniques, par la simulation par éléments finis et la modélisation, pour évaluer et […]