Automatiser l’inspection des matériaux composites, un enjeu stratégique pour l’université de Sheffield
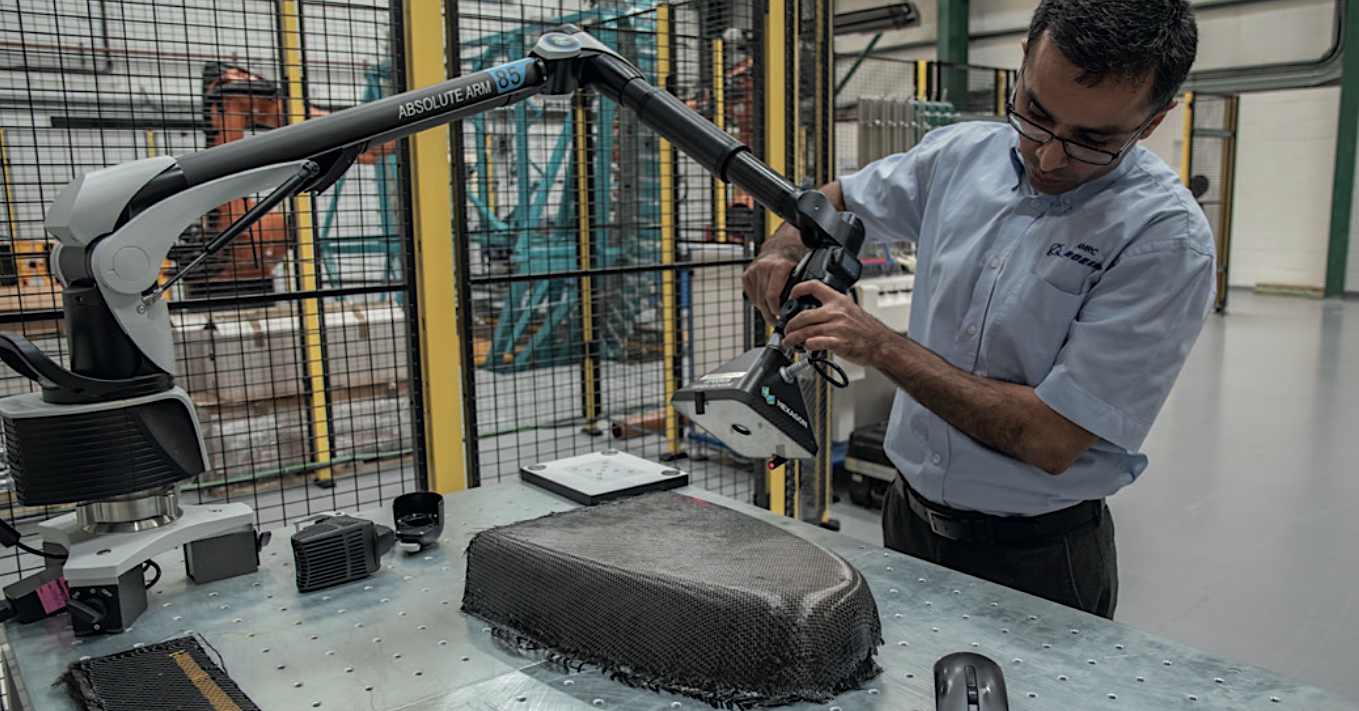
Les contrôles qualité pendant le placement des fibres ont une importance vitale et l’unité Composites du centre de recherche en fabrication avancée de l’université de Sheffield en sait quelque chose. Cette structure de R&D implantée dans une annexe de l’usine du futur de l’AMRC (University of Sheffield Advanced Manufacturing), à Rotherham (UK), réalise des recherches en relation avec la fabrication et l’usinage de composants composites, notamment de pièces hybrides associant des métaux et matériaux composites de haute performance dans la même structure. Plus précisément, cette unité réalise des composants ultra-légers à partir de matériaux composites de nouvelle génération, des matériaux de plus en plus utilisés dans l’aéronautique, l’industrie automobile et marine par exemple. « Notre clientèle est très variée. Elle comprend de grandes entreprises aérospatiales, comme Airbus, Boeing, Rolls Royce et BAE Systems, et des constructeurs automobiles, tels que McLaren et Toyota Motorsport, explique Zeeshan Qureshi, ingénieur de recherche principal au sein de l’équipe Analyse de conception et d’automatisation des composites. Mais elle ne se limite pas à des fabricants d’équipement d’origine ou à des fournisseurs de rang 1 ou 2. Nos prestations s’adressent aussi à des PME locales, que nous aidons à résoudre des problèmes de fabrication et de conception, et à devenir plus compétitives sur leur marché ».
Mais en matière d’inspection, les défis sont nombreux. Les fibres posées doit se faire après la mise en place de chaque couche pour vérifier que l’orientation des fibres reste conforme aux paramètres définis. Comme les éléments composites de structures épaisses (dans l’aéronautique et l’automobile, ils sont constitués de dizaines de couches de fibres), ces contrôles peuvent être assez longs, surtout avec une méthode d’inspection classique où la vérification est visuelle avec une loupe ; une inspection manuelle qui représente 70 % du temps machine total voire davantage. C’est pourquoi l’unité de R&D a opté pour une solution d’inspection automatisée du groupe Hexagon et plus particulièrement sa solution Absolute Arm et ses différents modules de scanner laser. « Nous avons constaté qu’Hexagon avait conçu un système d’inspection de composites spécialisé dans la mesure de l’orientation des fibres, qui pouvait résoudre à notre avis un certain nombre de problèmes d’inspection », précise Zeeshan Qureshi. Hexagon a ainsi proposé un équipement comprenant l’Absolute Arm, le scanner laser RS5 et le système Vision 3D. Ce système repose sur un capteur intégré à une caméra détectant l’orientation des différentes fibres composites. Le système utilise l’Absolute Arm pour référencer les positions. Combinées avec les scans du scanner laser du bras de mesure, ces données d’orientation des fibres peuvent être intégrées dans un modèle tridimensionnel de la pièce inspectée avec le logiciel Explorer 3D.
En matière d’inspection, les défis sont nombreux. Les fibres posées doit se faire après la mise en place de chaque couche pour vérifier que l’orientation des fibres reste conforme aux paramètres définis
Connaître les défauts de pièces à l’avance
L’équipe a réussi à appliquer le système pour effectuer des contrôles d’assurance qualité dans le cadre de la fabrication de pièces composites, principalement en rapport avec l’orientation de leurs fibres. « Le système nous permet de valider nos conceptions et simulations pour que la pièce fabriquée soit conforme au but du développement. C’est donc une bonne étape de validation pour notre processus de conception et de fabrication. Nous utilisons principalement le système pour le tissage et le tressage, de même qu’après le processus de préformage. Ces opérations peuvent inclure le tissage ou formage final 2D, 2,5D et 3D de tissus secs avec des méthodes thermo-mécaniques. Après cette première phase, nous pouvons placer la pièce sur la station de travail et la scanner avec le nouveau système d’inspection de manière à générer un profil 3D de cette pièce. Ensuite, nous réalisons des images de la surface que nous venons de scanner. Au moyen des algorithmes avancés du logiciel, nous pouvons déterminer l’orientation des fibres, ce qui peut nous renseigner sur certains défauts de la pièce, le cas échéant. »
Le logiciel Explorer 3D permet une analyse facile de la géométrie de la pièce et de l’orientation des fibres.
En outre, le système permet d’intégrer les données d’inspection dans la fabrication pour améliorer les futurs cycles de production. « Dans un premier temps, nous pouvons essayer de corriger les programmes et de réduire ces défauts en effectuant une meilleure programmation », explique Zeeshan Qureshi. Mais, parfois, les défauts sont liés à la géométrie ou à l’état des matériaux. Ceux-là, on peut les réparer avec une procédure appropriée, en enlevant des couches ou sections définies et en les reposant sur la surface. Ce processus est suivi des phases de durcissement et de post-traitement. Ensuite, les pièces sont soumises à un contrôle non destructif pour déterminer si elles remplissent les paramètres d’assurance qualité définis. Enfin, le logiciel Explorer 3D intègre un algorithme permettant de détecter des orientations de fibre. « C’est très utile pour nous, car le fait de connaître la précision de l’orientation des fibres de la pièce, nous donne de précieuses informations pour nos conceptions et nous permet de déterminer la performance structurelle de la pièce fabriquée dans cet état. »
Lisi Aerospace et le Cetim nouent un contrat de R&D pour mieux maîtriser les assemblages vissés
À l’occasion du salon du Bourget 2025, Lisi Aaerospace, fournisseur mondial de solutions d’assemblage et de composants de structure pour l’aéronautique, et le Cetim ont officialisé la signature du contrat de collaboration de recherche Digifast. Ce projet de R&D ambitieux vise à développer, d’ici 2027, un équipement de mesure et de contrôle de la tension de serrage à la […]
V2i, expert en dynamique des structures et vibrations, un partenaire incontournable de l’aéronautique, du spatial, de la défense et du ferroviaire
Forte de son expérience et de ses laboratoires accrédités ISO/IEC 17025:2017 (BELAC 666-TEST), V2i propose une offre complète : simulation numérique, essais vibratoires haute capacité, analyses modales et monitoring en temps réel. Grâce à ses moyens d’essais de pointe et à un environnement ISO 7, l’entreprise garantit des résultats fiables et précis, répondant aux exigences […]
Opton Laser, nouveau distributeur en France de Manx Precision Optics
Opton Laser International, distributeur français d’équipements photoniques implanté aux Ulis, en Île-de-France, a été nommé en juin distributeur français de Manx Precision Optics (MPO), fabricant situé sur l’Île de Man et spécialisé dans les optiques laser haute énergie avec des traitements à seuil de dommage laser élevé (LIDT). Selon les termes de l’accord, Opton Laser […]