Fabrication additive : un vélo singlespeed ultra-léger issu de l’impression 3D
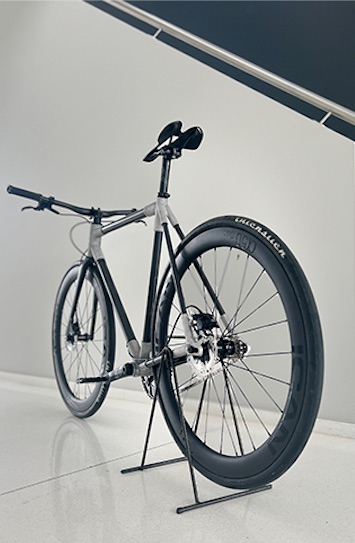
L’équipe de développement du logiciel industriel CoreTechnologie (CT) a créé un vélo incroyablement léger et économique à partir de composants en aluminium imprimés en 3D et de tubes en carbone standard. La version singlespeed entièrement opérationnelle du vélo ne pèse que 7,1 kg est prête à rouler. Contrairement à la production usuelle de cadres en carbone, les étapes de travail simplifiées ont permis une production rapide, agile et automatisée.
Géométrie optimisée du cadre, construction sobre et design convivial
Les ingénieurs de CoreTechnologie ont combiné des pièces de liaison en aluminium (AlMgSi10) imprimées en 3D et des tubes en carbone extrêmement légers fabriqués par les imprimantes de la société Carbonforce. Les tubes ont été assemblés à l’aide d’un adhésif bi-composant ultra-résistant issu de l’industrie aéronautique.
Le projet a été réalisé en un temps record de deux mois – de l’idée au prototype prêt à rouler. L’équipe de CT a optimisé la conception sur la base d’une géométrie de cadre existante de 56 centimètres et l’a perfectionnée à l’aide de différents rendus 3D. Grâce à une conception ingénieuse des pièces du cadre, cette version singlespeed peut également être équipée de vitesses.
La flexibilité rendue possible par la conception assistée par ordinateur (CAO) associée au processus d’impression 3D SLS ont permis d’obtenir un design particulièrement léger et épuré qui, grâce à ses caractéristiques de conduite, représente une contre-tendance par rapport aux vélos électriques lourds et techniquement complexes.
Produire des objets de consommation courante de manière économique
Dans le cadre de ce projet, le développeur a utilisé son logiciel 4D_Additive pour optimiser l’épaisseur des parois, générer des textures de surface et réaliser la production en douceur des pièces imprimées en 3D sur la machine SLM du partenaire de service FKM.
Lors des essais, ce vélo imprimé en 3D a fait la preuve de sa robustesse, de sa résistance et de sa maniabilité sur différents types de chemins. Avec ce projet et le prototype qui en résulte, l’équipe de CoreTechnologie montre qu’avec l’aide des logiciels et du matériel actuels, la production d’objets complexes de consommation courante est possible de manière économique, rapide et agile, indépendamment des chaînes d’approvisionnement vulnérables.
Webinaire CADFEM sur le GPU pour la simulation numérique le 25 septembre
Le webinaire CADFEM intitulé « Quel est l’intérêt du GPU pour la simulation numérique ? » se tiendra le 25 septembre à 11heures. Ce webinaire en partenariat avec FRA-SYS, constructeur hardware, couvre tous les aspects du calcul GPU en allant du fonctionnement même de la carte graphique et son intégration jusqu’à l’accélération potentielle que le […]
Climats innove avec une technologie de refroidissement au CO₂
Climats, une marque française pionnière dans le domaine de la simulation environnementale, a récemment développé une technologie de refroidissement utilisant le R-744 (CO₂) pour se conformer aux nouvelles réglementations de l’Union Européenne sur les gaz réfrigérants. À partir du 1er janvier 2029, les récentes normes exigent que les réfrigérants utilisés sous -50 °C devront avoir un […]
Comsol France sera présent cet été au Congrès français de mécanique 2025
Comsol, l’éditeur des logiciels Comsol Multiphysics, Comsol Server et Comsol Compiler, sera présent lors de la 26e édition du Congrès français de mécanique, qui aura lieu du 25 au 29 août prochain à Metz. Cet évènement est organisé par le Laboratoire d’étude des microstructures et de mécanique des matériaux (LEM3) en partenariat avec le Laboratoire […]